Mining Career Pathways A 2025 Guide for Metallurgists and Process Engineers
Mining Career Pathways A 2025 Guide for Metallurgists and Process Engineers - Future Mining Salaries and Career Growth Paths Through 2027
The mining sector is expected to see substantial shifts in career paths and compensation levels through 2027. A wide range of high-paying positions will be available, especially for specialists like geologists, engineers, and metallurgists, as the industry prioritizes technological advancements and improved resource extraction methods. Although some job displacement is anticipated, affecting roughly 20% of the workforce, this rate is considerably lower than in other energy sectors, implying a more secure future for mining careers. Staying competitive will require ongoing professional growth and building professional connections as the field changes and encounters new obstacles. Looking ahead, a proactive approach to workforce planning is crucial to ensure the mining industry maintains a capable and resilient workforce capable of meeting future demands.
Looking ahead to 2027, the mining sector seems poised for a substantial growth in the demand for skilled professionals, particularly driven by the integration of technology. We're seeing an increasing need for expertise in automation and data analysis, suggesting a shift in the types of roles and competencies that are most valuable. This projected 20% increase in demand for skilled labor suggests a positive outlook for career opportunities in this sector.
It's interesting to note that metallurgists and process engineers are anticipated to experience above-average salary increases, at roughly 4-5% annually. This stands in contrast to other engineering fields, potentially indicating a growing recognition of their critical role in optimizing mining operations.
The concept of remote operation centers is gaining traction. It’s fascinating to consider how this will influence traditional workforce models and job opportunities. Could we see a decentralization of workforce, potentially leading to new career paths focused on remote management and control?
Upskilling in emerging technologies like machine learning and AI appears to be crucial, not just a bonus. As these tools become more integrated into mining operations for tasks like predictive maintenance and optimization, professionals lacking these skills might find themselves at a disadvantage.
Virtual reality training is gaining traction, offering a new approach to personnel development. The positive impact on training retention rates is promising, signaling a potential revolution in how skills are imparted within the industry.
Geologists seem to be experiencing an upward trend in salaries, even potentially surpassing traditional mining engineers in some instances. This suggests a growing recognition of the economic value of resource discovery, a cornerstone for any mining project.
While established roles remain, we're witnessing the emergence of new ones, such as data scientists within mining companies. This fusion of conventional mining knowledge and data analytics points towards a need for individuals with hybrid skill sets.
The looming retirement of a substantial part of the workforce is creating a window of opportunity. With around 30% of positions potentially vacant, younger engineers may have a quicker path to leadership roles compared to previous generations.
Resource-rich nations are making significant investments in research and development within their mining sectors. This trend could invigorate local talent and generate new career pathways in regions previously under-developed in this area.
The expanding demand for advanced metallurgy, particularly related to the production of electric vehicle batteries, could open up specialized career paths for metallurgists. This highlights how specific expertise can become highly valuable within specific niches within the broader mining industry.
Mining Career Pathways A 2025 Guide for Metallurgists and Process Engineers - Emerging Automation Technologies Impact on Process Engineering Jobs
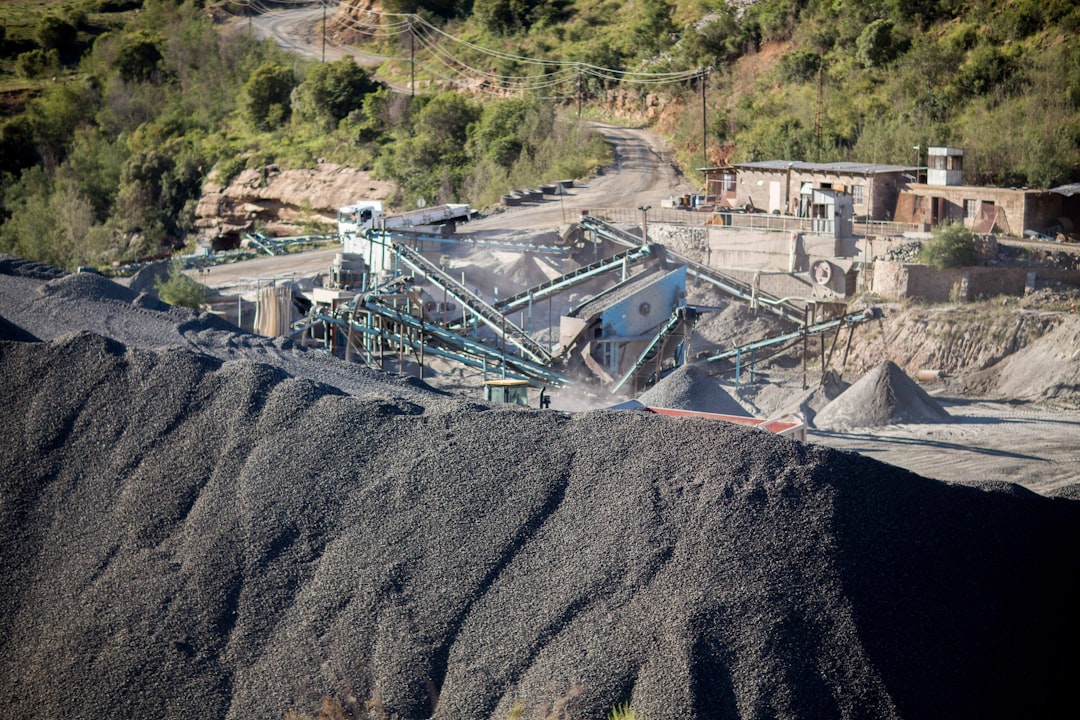
The rise of automated systems is fundamentally altering the nature of process engineering roles within mining. While some tasks previously handled by engineers are now being automated, this shift isn't necessarily leading to job losses. Instead, it's prompting a transformation in the skillset required for process engineers. The focus is shifting towards managing and optimizing automated systems, interpreting data, and ensuring seamless integration of these technologies into existing operations. This transformation is fueled by a broader push towards digitalization in the mining sector, with the goal of boosting efficiency, improving safety protocols, and advancing sustainability initiatives.
This means that the future of process engineering in mining will demand a blending of traditional mining expertise with proficiency in advanced technologies. The emergence of automation is creating new positions that require a hybrid skillset, a combination of understanding the physical processes involved in extraction and the ability to work with sophisticated automated systems. This necessitates a continuous learning mindset for aspiring process engineers who want to thrive in this dynamic sector. It's crucial that individuals entering this field recognize the ongoing evolution of mining and the necessity of adaptability to remain competitive in a changing job market.
The increasing use of automation is reshaping the skillset landscape for process engineers. It's becoming increasingly clear that a strong understanding of complex algorithms and programming languages, which haven't traditionally been core to many engineering educations, is becoming crucial. It's fascinating to consider how this shift will affect the types of engineers needed in the future.
Estimates suggest that roughly half of the tasks currently handled by process engineers could be automated by 2025. While this might seem daunting, it also implies that engineers will be able to focus their energy on higher-level decisions and strategic planning instead of routine operational tasks. This shift could potentially redefine the role of a process engineer.
Digital twins are having a remarkable impact on mineral processing design and optimization. Engineers are now able to model and optimize processes in real-time, drastically reducing the gap between design and implementation. It's intriguing to contemplate how this will affect traditional project lifecycles.
The automation of QA/QC processes has yielded notable improvements in efficiency. Studies show that error rates in data analysis have dropped by as much as 90%. This is changing the focus for many roles – verifying and validating data is becoming even more vital. It's prompting me to question how this change will impact the type of professional development and educational pathways that will be most useful.
It's becoming apparent that the role of the process engineer is evolving. They are, in a way, becoming systems integrators, demanding a more multi-disciplinary skillset that combines traditional engineering with elements of computer science and operations management. I wonder what this will mean for collaboration between engineering departments and other fields within mining companies.
A recent study found a strong link between automation investment and improved productivity – up to 30% in some instances. There's also a noticeable increase in job satisfaction when engineers are freed from mundane tasks and can focus on innovation. It makes one wonder if this trend might alter how the mining industry attracts and retains engineering talent.
The collaboration between process engineers and data scientists is growing increasingly vital. This fusion of traditional engineering expertise with machine learning and data analytics is fostering new hybrid roles. It's fascinating to consider how this shift will transform teams and the dynamics within mining operations.
Automation is not simply about improving efficiency. It's creating new positions focused on managing these automated systems. This means that engineers will need to continuously update their skills to remain relevant. The future engineer will need to be flexible and willing to learn.
The changes brought by automation suggest a restructuring of job functions. Supervisory roles are emerging to oversee automated systems, adding a new layer of complexity to career paths. It will be interesting to see how leadership roles evolve and the skillset required for them.
One of the most striking impacts of automation is the potential for dissolving traditional geographic constraints. Remote teams can manage mineral processing plants, leading to a reassessment of both local job markets and the very nature of engineering work within the mining industry. It's truly a transformative time, and it's exciting to see how the mining landscape evolves in the coming years.
Mining Career Pathways A 2025 Guide for Metallurgists and Process Engineers - Environmental Compliance Requirements for Metallurgists in 2025
By 2025, the environmental compliance landscape for metallurgists will be significantly more complex and demanding. Metallurgists will need to be increasingly aware of and adaptable to the evolving regulations, especially from agencies like the Environmental Protection Agency (EPA). The growing emphasis on Environmental, Social, and Governance (ESG) factors will also impact their work. This means that metallurgists will not only be responsible for the traditional aspects of their roles, like metal extraction and processing, but will also have to prioritize integrating environmentally friendly practices into operations. This constant need to balance economical aspects of mining with environmental protection will remain a significant hurdle, especially as new technologies and societal expectations change the sector. To thrive in this evolving environment, metallurgists will need to strengthen their skillsets, focusing on areas related to environmental regulations and sustainability. It's clear that transitioning towards environmentally conscious mining practices is not just a trend, but a necessity that will redefine the roles and obligations of metallurgists and the entire field.
By 2025, metallurgists will find themselves operating within a progressively intricate landscape of environmental regulations and compliance standards. This includes areas like electronic waste management, as the push for more advanced materials clashes with growing scrutiny over their eventual disposal.
The emergence of newer alloys and composite materials within mining will necessitate more rigorous testing and validation procedures. This means metallurgists will need to stay current with rapidly changing material specifications that have direct links to environmental compliance – a constant learning curve is practically guaranteed.
With the increasing adoption of advanced sensors, metallurgists will be increasingly involved in interpreting data about emissions and effluent streams. This shift towards data analysis demands a deep understanding of compliance metrics and environmental reporting protocols.
We can expect international collaborations to complicate the environmental compliance picture for metallurgists. Different regions have their own unique requirements, pushing individuals to broaden their understanding of global regulations and best practices – a kind of regulatory patchwork across the globe.
Machine learning will likely play a bigger role in compliance monitoring. This offers the potential to predict potential regulatory breaches. But, this also creates a need for a critical eye when reviewing data, as overreliance on algorithms without human oversight could lead to problems.
There's a growing emphasis on circular economy principles, urging metallurgists to design processes that not only adhere to environmental laws but also enhance material reuse and recycling from the outset. This shifts their focus from traditional manufacturing towards creative process design.
Compliance audits will likely leverage blockchain technology for improved transparency and traceability of raw material origin and processing methods by 2025. Metallurgists will need to ensure thorough and accurate process documentation to meet these changing requirements.
The anticipated rise in remote and automated mining facilities introduces new compliance hurdles. Metallurgists will face the challenge of ensuring these technologies adhere to environmental regulations without sacrificing operational efficiency. It's a difficult balance to strike.
As regulatory bodies push for real-time emissions reporting, metallurgists will need to embrace advanced reporting tools and software built for dynamic compliance tracking. Adapting to these changes will be crucial.
Finally, a trend towards peer-reviewed compliance practices could emerge. Here, metallurgists would engage in collaborative reviews of their respective operations and challenges. This suggests a future where shared knowledge is highly valued in navigating the rapidly evolving compliance landscape.
Mining Career Pathways A 2025 Guide for Metallurgists and Process Engineers - Key Digital Skills Required for Mining Process Engineers
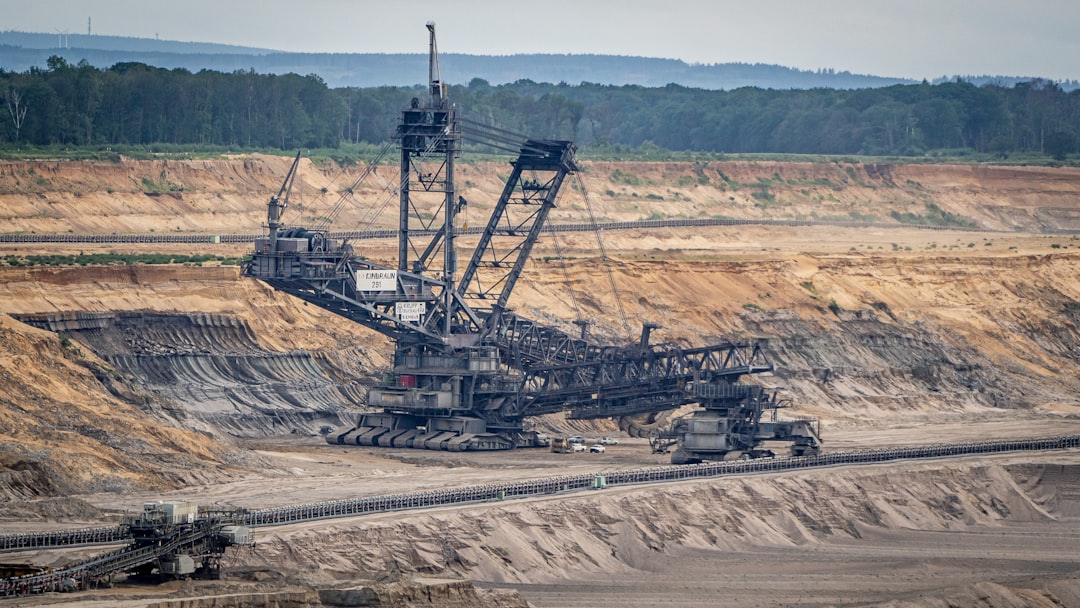
The mining industry is undergoing a digital transformation, and process engineers are at the heart of this change. The increasing adoption of automation and data-driven technologies is fundamentally altering the skillset needed for success in this field. Process engineers are no longer just focused on traditional mining tasks; they're increasingly involved in managing and optimizing automated systems. This necessitates a strong foundation in data analytics and the ability to interpret complex datasets. Furthermore, the emergence of automation has made proficiency in programming languages and sophisticated algorithms vital, requiring engineers to step beyond their traditional expertise and embrace new areas of knowledge.
The evolving landscape also necessitates continuous learning. Engineers must stay current with rapidly advancing technologies, fostering a mindset of adaptability and a willingness to collaborate with experts from fields like data science. As digital twins, real-time monitoring systems, and other digital tools become integrated into mining operations, the need for individuals capable of managing these complex systems grows. This change is blurring the lines of traditional process engineering, creating a demand for more versatile professionals who can bridge the gap between the physical and digital aspects of the mining process. Essentially, the future of process engineering in mining requires a hybrid skillset – a blend of traditional engineering expertise and an aptitude for navigating the intricate world of digital technologies.
The mining process engineering landscape is undergoing a rapid transformation, demanding a new set of digital skills alongside traditional engineering knowledge. We're seeing a growing need for proficiency in data analytics, a shift from simply collecting data to leveraging it for informed decision-making and optimization. Tools like Python and R are becoming increasingly important, allowing engineers to not only analyze data but also to automate tedious tasks and build predictive models. This development, while promising, brings about questions about how the current generation of mining engineers is adapting to this shift in responsibilities.
The concept of digital twins is gaining traction, with engineers now able to create virtual representations of mining processes. This has significant implications, especially in reducing the risk associated with trial-and-error methods during the design and implementation stages of new technologies. It's intriguing to consider how this evolving technology could change the way we approach process engineering within the mining industry.
A notable shift is the evolution of the process engineer's role into a kind of systems integrator. This involves coordinating and understanding the interactions between a variety of automated systems, requiring a broader knowledge base that blends traditional engineering with aspects of computer science and information technology. I wonder about the implications for collaboration between different departments within mining companies—will there be a need for re-structuring and increased communication channels?
Cybersecurity is no longer a peripheral concern, but a core requirement. With mining operations becoming increasingly reliant on networked systems, engineers must be able to assess potential vulnerabilities and build robust defensive mechanisms. This necessitates an awareness of both current and future cyber threats—an ongoing challenge given the speed at which these threats evolve.
The widespread deployment of IoT devices in mining means engineers need to grasp how advanced sensor technologies can be integrated into operations. This increased focus on data collection will enable more precise monitoring of mineral processing efficiency, leading to enhanced insights into equipment health. It's important to note, however, that this transition towards data-driven decision-making needs a thorough examination of its implications for existing operational models.
It's vital for engineers to think critically about how automation impacts the human element of the workforce. This involves understanding the delicate balance between human oversight and automated systems, ensuring that safety and quality standards are consistently met. It raises important questions regarding the nature of future work in mining and the evolving roles of engineers.
Furthermore, effective project management skills are becoming increasingly essential as engineers grapple with more complex projects involving diverse technologies and teams. The ability to organize resources and manage cross-functional groups is crucial to ensure smooth project completion. This will likely influence how the future of mining engineering education evolves.
Staying up-to-date with regulatory changes impacting the mining sector is another crucial aspect of a modern process engineer's role. It's no longer enough to focus solely on the technical side, understanding how these evolving regulations intersect with automation and digital practices is equally critical.
Finally, the growing importance of artificial intelligence in mining necessitates increased collaboration between process engineers and AI specialists. This collaboration is key to leveraging machine learning algorithms for optimizing operations, pushing the boundaries of innovation within the sector. While the potential for improved efficiency is great, we need to critically analyze how human expertise can best be combined with these advanced technologies to minimize risks.
It's an exciting time for mining process engineering, one where adaptability and a willingness to learn are key to success. The industry is transforming before our eyes, prompting a constant need for engineers to evolve and embrace new technologies. The next decade will be one of significant change in the mining sector, demanding a workforce that is agile, technically skilled, and collaborative.
Mining Career Pathways A 2025 Guide for Metallurgists and Process Engineers - Remote Work Options in Metallurgy and Process Engineering
The mining industry's increasing reliance on technology and the desire for more flexible work arrangements has spurred a notable rise in remote work opportunities for metallurgists and process engineers. A substantial number of remote positions, particularly in research, environmental engineering, and various technician roles focused on data collection and monitoring, are now available, reflecting a shift towards incorporating remote capabilities within traditional engineering functions. This expanding landscape is leading to new types of roles that emphasize specialized skill sets in automation, data analysis, and technology integration, making continuous learning and adaptation a critical part of professional development. Furthermore, the rise of hybrid work models, blending remote and on-site responsibilities, is becoming increasingly common, potentially reshaping how teams collaborate and how mining operations are managed. While this transition opens up new career avenues, it also highlights the continuing need for professionals to build strong networks and participate in industry organizations to stay informed and advance their careers in this evolving sector. Navigating these changes will require a flexible approach and an understanding of how the mining industry is being impacted by broader technological trends.
The increasing adoption of remote technologies in the mining sector is opening up new opportunities for metallurgists and process engineers. Drones, satellite imagery, and other remote sensing tools are enhancing our ability to monitor operations from afar, giving engineers a more comprehensive view of processes and facilitating faster decision-making. Cloud technology and data sharing platforms are breaking down geographical barriers, allowing engineers in disparate locations to collaborate in real-time, analyze data collectively, and work together on complex problems.
Interestingly, the rise of digital twins within metallurgy is providing a powerful tool for remote engineering. By creating virtual representations of processes, we can run simulations, predict equipment failures, and troubleshoot problems without needing to be on-site. This shift towards remote capabilities is naturally changing the required skillset. Engineers need to become proficient in the software and platforms that facilitate remote control and data management, adding a new dimension to their existing metallurgical and process engineering skills.
Companies embracing telecommuting policies for metallurgists and process engineers often report gains in both job satisfaction and productivity. These arrangements, leading to better work-life balance, are proving to be a retention strategy for valuable engineers. However, with increased reliance on remote systems, cybersecurity becomes a critical issue. Mining operations are becoming increasingly vulnerable to data breaches, and while IT specialists handle much of it, engineers increasingly need to understand security protocols.
Virtual collaboration tools are fostering a new era of problem-solving across diverse teams. Engineers can participate in global discussions, run simulations together, and interact with virtual models in real-time, leading to improved outcomes and faster innovation. The concept of remote operational centers is also gaining traction. From these hubs, metallurgists and process engineers can effectively manage multiple mining sites across various time zones and optimize resource allocation.
Artificial intelligence is also changing the way we think about remote work. Machine learning algorithms are allowing us to make predictions about equipment failures and process bottlenecks, enabling proactive management and reduced downtime. We are witnessing the emergence of new, remote-specific roles. Remote systems integrators and virtual process optimization specialists are in demand, demonstrating a growing need for individuals who blend traditional engineering expertise with digital skills.
It's certainly a fascinating time to be a metallurgist or process engineer. While the rise of remote work options presents some challenges, like cybersecurity risks and the need to adapt skills, it also opens up exciting new avenues for collaboration, innovation, and career advancement. It remains to be seen how this evolving landscape will shape the future of our profession.
More Posts from skymineral.com: